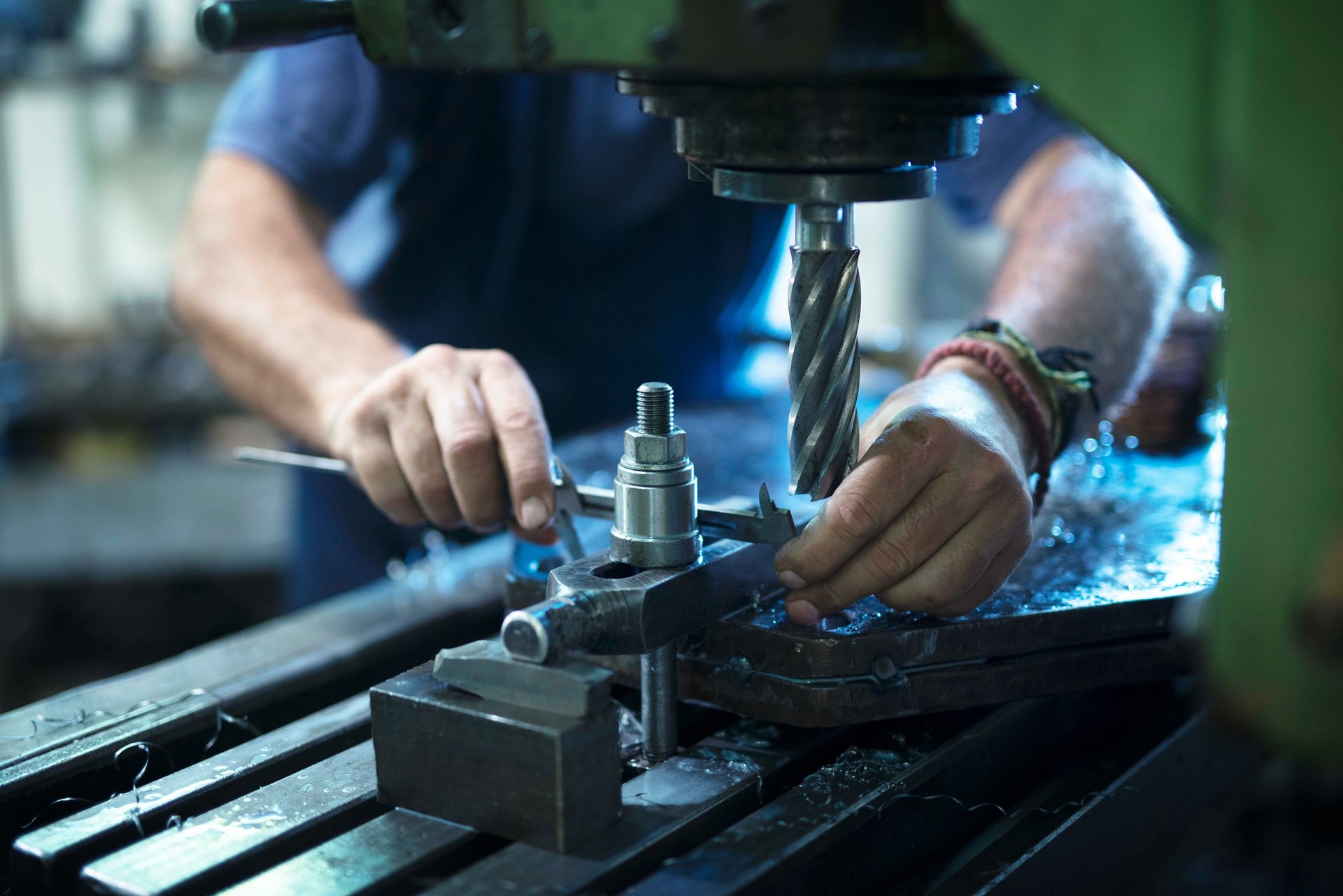
22+ YEARS
STRONG
LEGACY
OUR STORY
ABOUT US
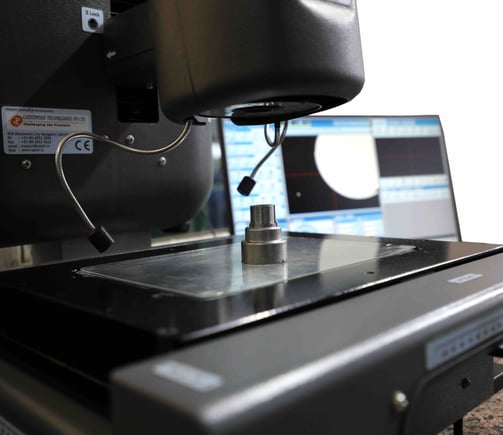

Founded by R.S Shekhawat as small workshop for sheet metal components with 10 employees in year 1997 at Ballabgarh, Haryana. Since then building on our values of providing unprecedented quality in our products, we have grown modestly to 600 employees, spread across 4 locations in India.
Our capability has grown from sheet metal to plastics, tubular and assembly components for the major OEMs of automotive industry in India and abroad.
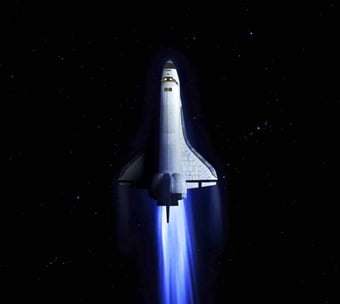
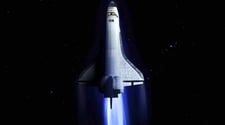
VISION
MISSION
Building high quality components that meet customer expectations at a competitive price.
To be the world leader for automotive components & first choice of OEMs when it comes to automotive components.
OUR MANAGEMENT
LEADERSHIP
Our strength lies in our individuality. Set up by R.S Shekhawat, Jayant Shekhawat- the team strives to bring in the best in all departmets, from tool design to production and sales.
A COLLECTIVE, THAT MAKES DREAMS COME TRUE
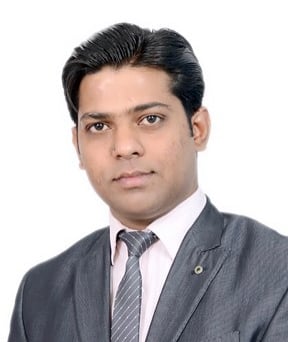
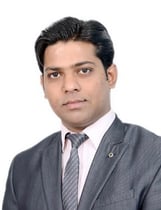
R.S Shekhawat
Jayant Shekhawat
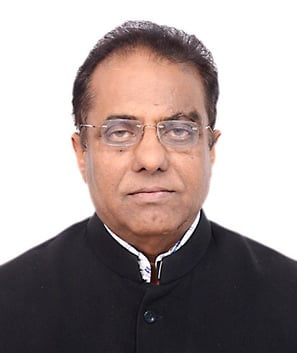
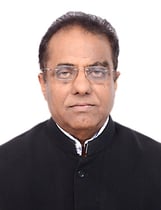
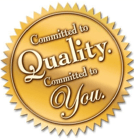

OUR QUALITY
QUALITY POLICY

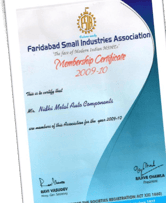
Our commitment to quality and the satisfaction to customers is the fundamental principle at Nidhi Metal
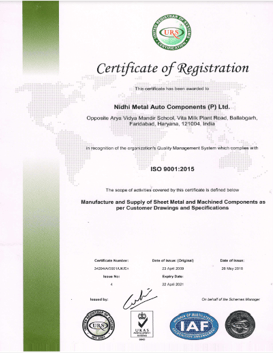
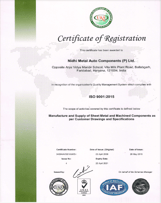
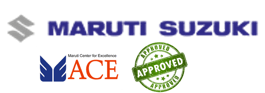
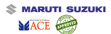
We are dedicated for customer satisfaction by continuously striving for excellence in productivity, quality and delivery with a sole mission of “Zero Defect Product” and “Total Customer Satisfaction”.
QUALITY OBJECTIVES
Regular Verification for compliance of International Quality Management system ISO 9001:2015 through audits.
To reduce manufacturing process rejection.
To use the resources in such a way that cost competitiveness can be achieved.
To establish quality culture through employee training
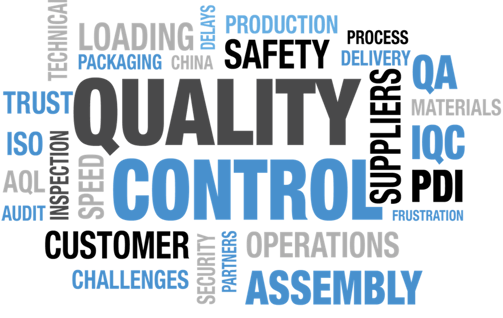
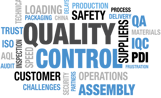
QUALITY CONTROL
We take quality very seriously. Our Quality Assurance (QA) department is an essential group of individuals who consistently test and retest the manufactured parts to every dimensional callout on the drawing.
With a state of the art facility and industry standards our QA department ensures perfect quality each time.
Along with the diligent duties of checking our manufactured parts, our QA department works closely with incoming raw materials inspecting every shipment for defects. When parts do have to be returned (RMA) our QA personnel ensures that the customer receives exactly what they need and strive to document the problem to insure that it doesn't happen again.
Since we offer a vast variety of plating options in our components the QA department also works in conjunction with different plating suppliers. Constantly checking classification and specifications against all standards where applicable.
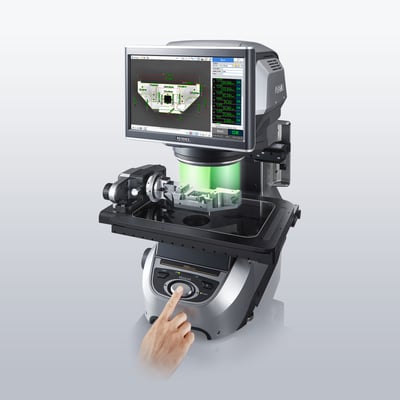
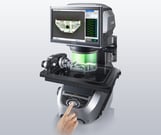
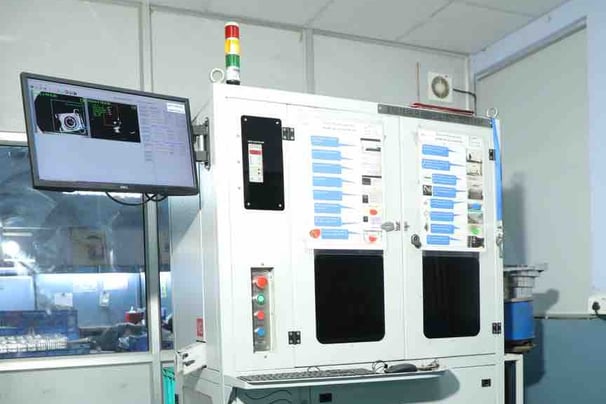
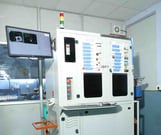
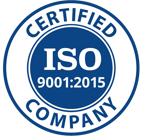

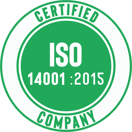

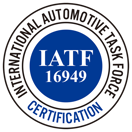

Corporate Office & Plant III
Plot 293, Sector 68, IMT Faridabad, India
Contact Us
info@nidhimetal.com
© Nidhi Metal Auto Components Private Limited
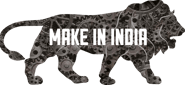
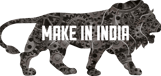
Plant I
Arya Nagar, Ballabhgarh Faridabad, 121004
Plant II
No. 11C, Industrial Park IV, Begampur, Haridwar, 249402
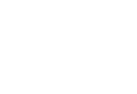
